- Title
-
Managing supply and demand in a high-risk world
- Section
- Blog
- Summary
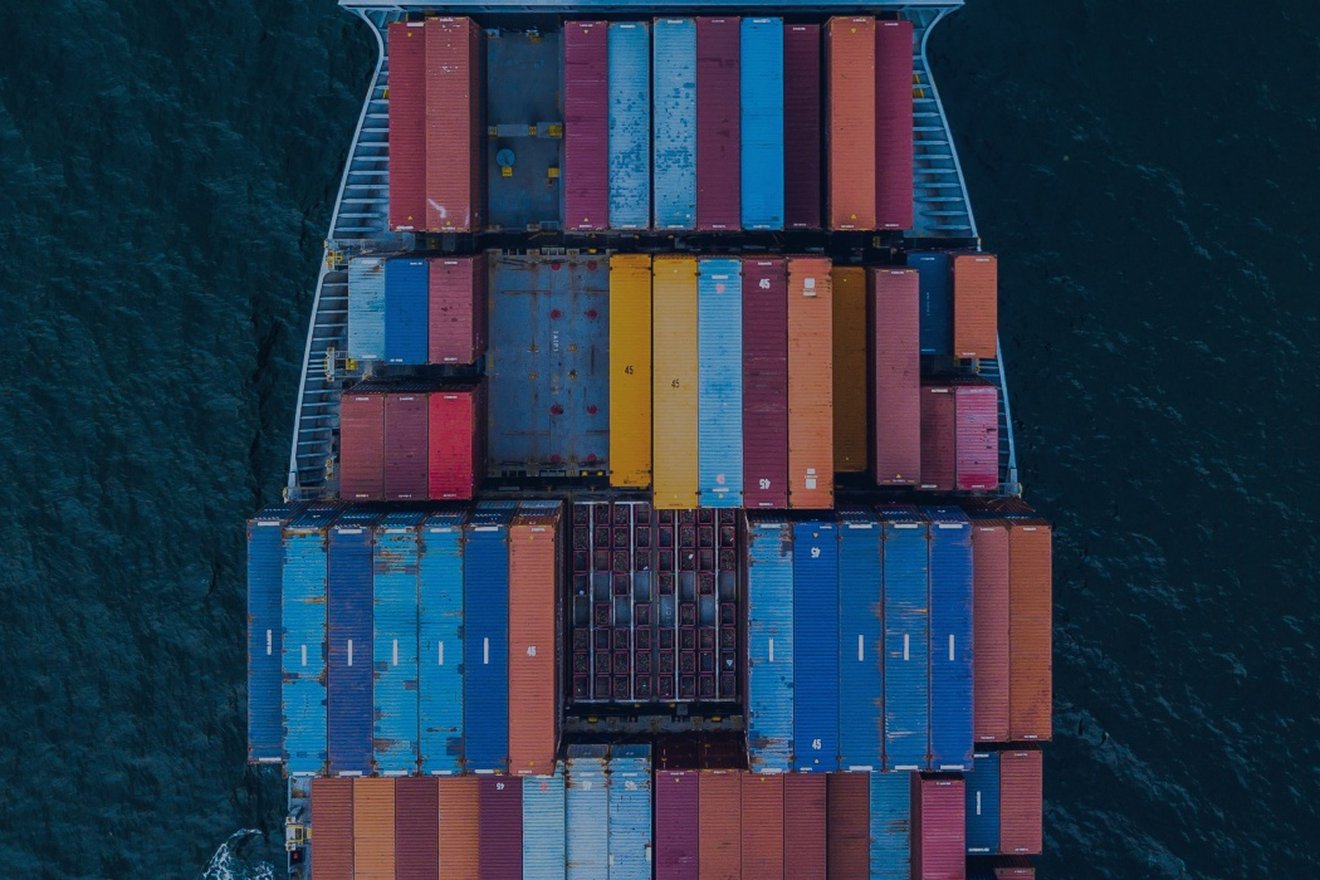
Port congestion, freight delays, and surging demand have been at the forefront of the global supply chain news agenda in recent months. To this, we now need to add Russia’s invasion of Ukraine. With countries around the world rallying in support – many have imposed a range of economic and other sanctions on Russia – the supply chain disruption and economic impact will be significant.
Shortages of raw materials had already been an issue coming out of the COVID pandemic but the crisis in Ukraine is likely to exacerbate this, given that Russia and Ukraine are significant exporters of a range of commodities. Notably, this includes Russian oil and gas – already the subject of a partial embargo by Western nations – but it also includes ammonia and fertiliser products; corn, wheat, and other crops; and a variety of metals. Prices for these products have spiked following the invasion and are likely to remain high until the crisis is resolved. We should also expect a range of second-order problems to emerge as price and supply challenges work their way through the supply chain. For example: Ukraine and Russia are both significant exporters of neon gas, used in the manufacture of microchips. This has led to a recent warning from the US government about the potential impact on the chip industry from the crisis (and this at a time when the industry is struggling to ramp up supply to meeting demand coming out of COVID).
The world isn’t standing still. Since the height of COVID – which saw everything slow down (including shipping) – demand has rebounded faster than any of us thought. The release of pent-up demand is now resulting in huge spikes in spending, and this – when combined to the current crisis – is having a knock-on effect when it comes to global shipping capacity and availability of commodities.
Demand in the face of adversity
Whilst inflation was inevitable, this is all happening against a backdrop of increasing labour shortages across a range of sectors. HGV drivers continue to be a prime example of this, with a recent survey of 20 countries conducted by the International Road Transport Union (IRU) indicating up to 25% of jobs unfilled, with parts of Eurasia and Europe hardest hit. The causes of labour shortages vary from sector to sector but in the UK, for example, they are typically a result of some combination of COVID-19, Brexit, and specific sectoral issues.
Nevertheless, whether it is a labour shortage, the ongoing impacts of COVID lockdowns, or the crisis occurring in Ukraine, we are now living in an increasingly volatile world where one-off disasters or “black swan” events seem to be becoming the norm. While each of these events may vary in specifics, the consequences are much the same, begging the question: Does “business as usual” still exist as a useful concept when thinking about supply chains, or should we accept that the world is becoming riskier and plan our supply chains accordingly?
Preparing for a more complex norm
Rather than seeing these events or circumstances as a “one off”, organisations must adapt their business models to ensure resilience across the entire supply chain. This, for many, will require a change in mindset.
Whilst a business model based on pursuing revenue and squeezing costs may have worked in a low-risk world, this approach no longer makes sense. Instead, organisations must focus on building in resilience where they can. This may require sourcing multiple contracts and diversifying suppliers or onshoring manufacturing operations to ensure production takes place closer to the customer. While this may be less cost-effective initially, these considerations can limit disruption when the next crisis emerges. Rather than pursuing revenue for its own sake, businesses would be wise to pursue good margins that factor in these additional costs and make way for a more resilient supply chain.
Along with this change in mindset, there also needs to be an infrastructure investment to keep pace with growth and a rebounding economy. Until now, there has been a lag, and investment is needed urgently in order to catch up.
As we move towards a more complex supply chain, companies need to get smarter at understanding changes to demand, and this requires smarter data and analytics. For example: previously, where port operators were geared around big seasonal trends, demand has become much more complicated, and we are seeing the demand for peak-like volumes all year round. Unfortunately, traditional forecasting models are not as predictable in this new normal – so, to keep up, global supply chains need to adapt.
No going back
There will be those that argue that after the last impacts of the pandemic passes, normality will return. However, as the Ukraine crisis – which seemingly came out of nowhere – shows, the world is changing, and companies need to adapt accordingly. The predictable, low-risk world of the 90s and early 2000s is coming to an end and, along with it, the simple “one-size-fits-all” supply chain.
In order to come out the other side of both current and future adversity, businesses need to understand that rather than a blip, a more permanent shift has taken place. Organisations must act now to review their existing supply chain model and determine whether it is fit for purpose in this new higher-risk world. Those that arm themselves with the tools and infrastructure needed for agility will be those that succeed.