- Title
-
Optimising a complex inbound supply chain for a post-merger food distributor
- Section
- Case study
- Summary
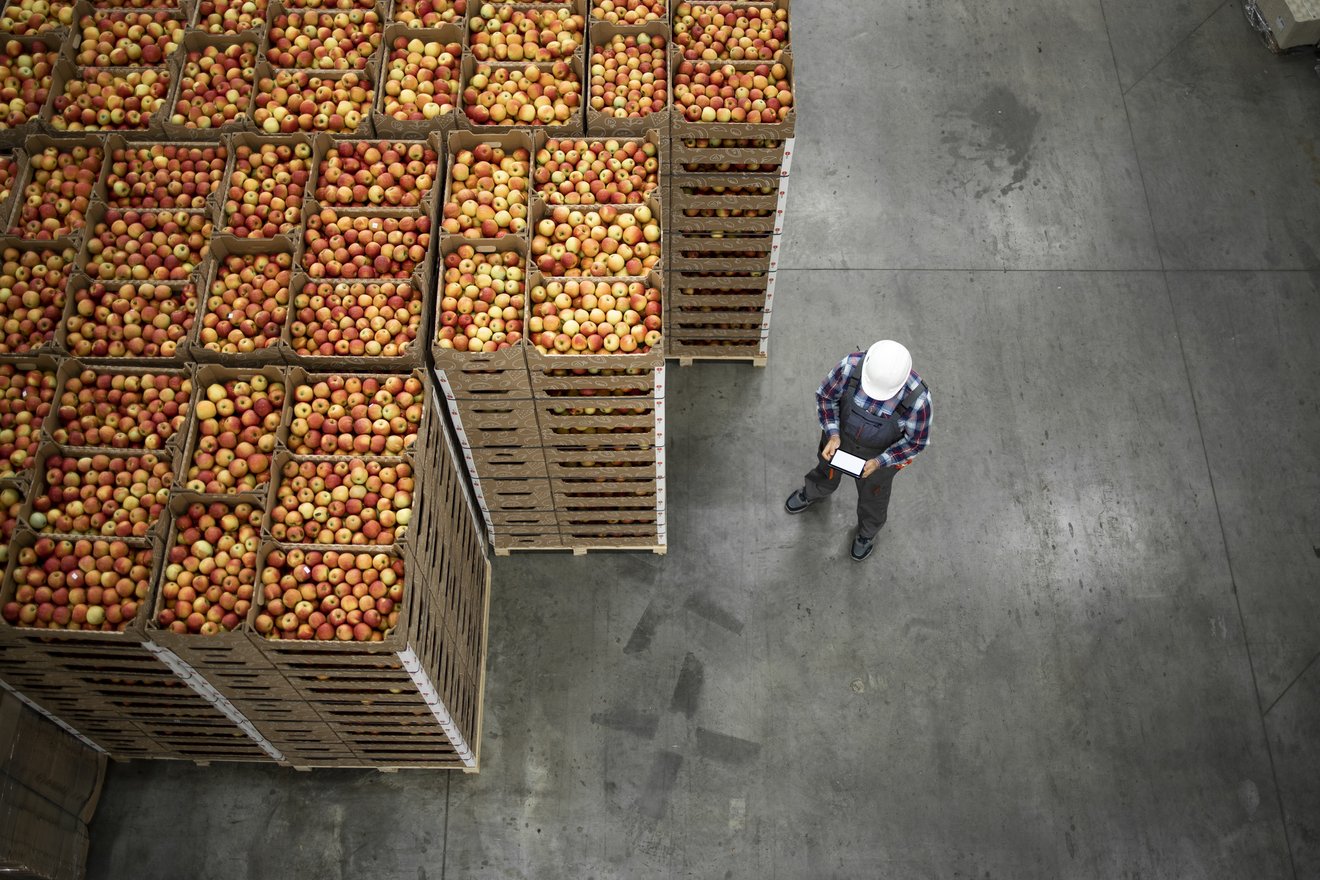
Our client is one of the world’s leading food distributors, with 300+ distribution facilities in more than 90 countries. It provides fresh, frozen, and ambient products to customers spanning across restaurants, healthcare and educational facilities, hospitality businesses, and wholesalers.
One of the client’s regions announced the merger of two subsidiaries and, despite its varied synergy initiatives, the combined group’s performance deteriorated in the early years of the merger. The source of this challenge? The merger resulted in a complex supply chain which involved more than 30 warehouses, 800 suppliers, 10,000 products, and 100,000 clients.
Following Efficio’s various successful engagements with the company’s other European subsidiaries, the regional group engaged us to optimise its inbound supply chain – particularly in relation to the demand function – all whilst navigating the disruptions created by COVID-19.
Results
In collaboration with Efficio, our client’s regional team:
- Set up reliable and accessible KPIs to evaluate success
- Established a new demand planning function, with an official forecasting system and a team redesign
- Implemented systems to ensure the longevity of the demand planning transformation: for instance, dedicated technologies such as a centralised control tower for stock replenishment with a clear inventory strategy and replenishment rules
Challenges and approaches
Rethinking the demand function
Our client faced various typical post-merger integration challenges – especially with its vast logistics network – with inconsistent inventory rules, process gaps, limited cross-functional cooperation, loss of knowledge, and no common reporting methodologies. These issues were aggravated by the COVID-19 pandemic, which highlighted the vulnerability of the regional group’s demand planning capacity and the need to give it greater attention.
Historically, only a limited part of the business had had a dedicated forecasting team and tool, with supply planners and buyers performing demand planning tasks on an unofficial, ad hoc basis.
To set our client up for success amidst abruptly changing customer demand, our joint team took steps to reposition the demand function to the heart of its operations and integrate innovative technologies into its systems.
Tackling the demand function transformation
This transformation took place across three phases:
- Phase 1 focussed on delivering performance transparency through clear KPIs and accessible dashboards as well as improving supplier performance management. We developed a temporary forecasting solution to manage our client’s vast portfolio of products across multiple delivery points, taking the uncertainties created by COVID-19 (such as lockdowns and school and restaurant closures) into account.
- Phase 2’s objective was to improve operational performance, while establishing the business case for the demand planning function, selecting the forecast solution from the market, and redesigning the broader inbound supply chain team. Indirect & inbound transport were also resourced to help finance the transformation.
- Phase 3 centred around ensuring the sustainability of the transformation: harmonising the replenishment process, implementing the selected forecasting tool, initiating the sales and operations planning (S&OP) process, introducing an issue resolution cycle, and working on network redesigning with the outbound team, with newly negotiated rates.
In a challenging mid-pandemic, post-merger integration project, a significant contributing factor to our client’s success was our integration with its procurement and supply chain team.
To protect the longevity of the successful transformation, we developed specialised digital tools for long-term use – ranging from a forecast solution to an inventory control tower – and continue to provide regular, ongoing staff training.
We’re here to help
If you would like to improve your supply chain function, related service levels or costs through insight or execution, please contact us by filling out the form on our Supply Chain Improvement service page.
PRINTABLE PDF