Benötigen Sie Hilfe in der Lagerhaltung und im Materialmanagement? Die Berater von Efficio unterstützen Sie gern bei der Transformation Ihrer Supply Chain.
- Title
-
Zurück aufs richtige Gleis: Transformation der Supply Chain eines Zugherstellers
- Section
- Fallstudie
- Summary
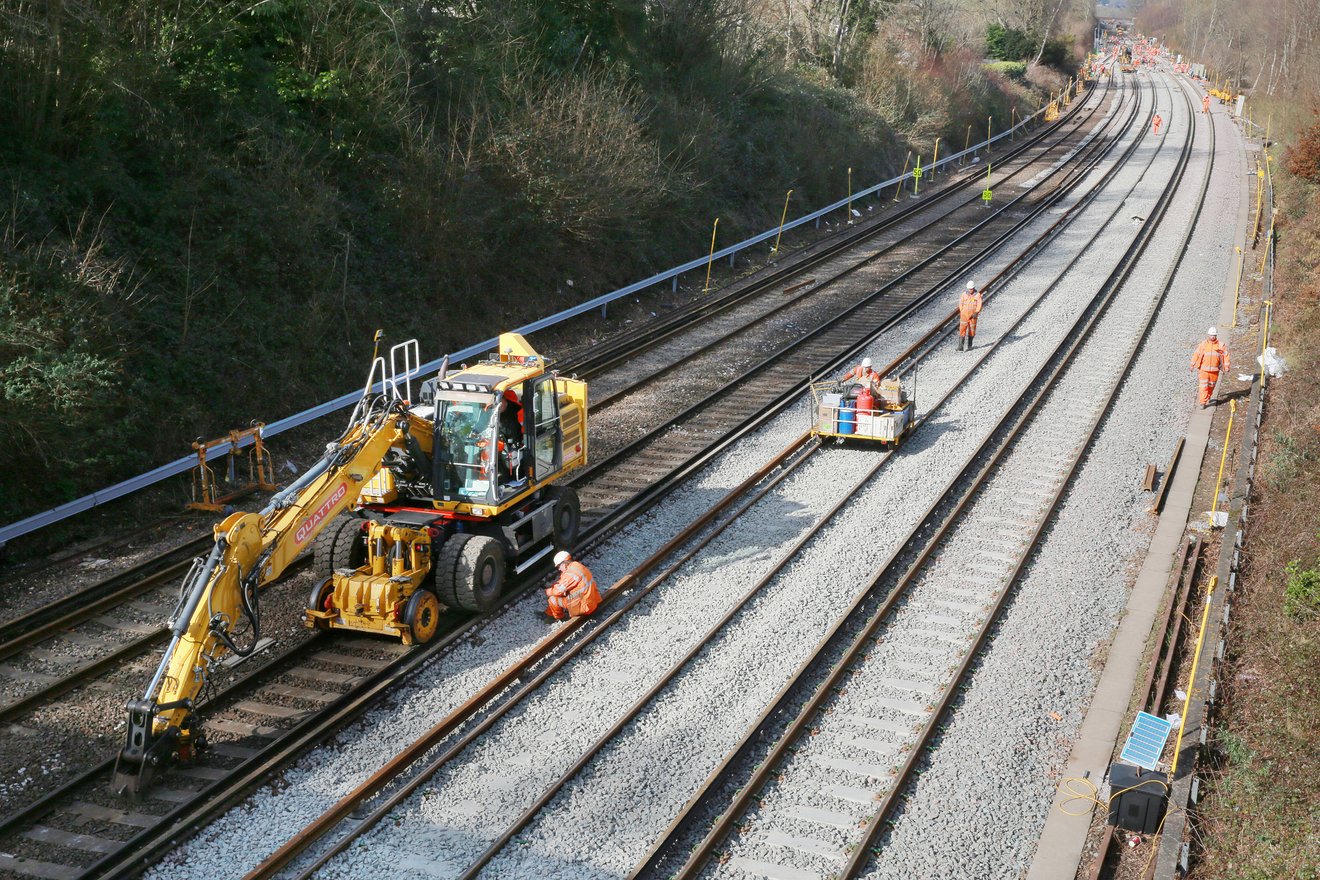
Ein führender Hersteller von Schienenfahrzeugen hatte erst vor Kurzem eine neue Produktionsstätte in Nordengland eröffnet – ein großer Erfolg für die gesamte Branche, die Region und natürlich den Hersteller selbst. Durch Herausforderungen beim Materialmanagement gerieten allerdings die Lieferfristen für neue Züge in Gefahr und es drohten erhebliche Verzugsstrafen.
Da die Materialverfügbarkeit (der Anteil der Artikel, die täglich auf der Produktionslinie verfügbar sind) deutlich unter den Zielvorgaben lag, gerieten Zeitpläne ins Wanken. Angesichts der bevorstehenden Fristen wurde Efficio beauftragt, die Probleme rasch zu identifizieren und zu lösen.
Efficio konnte die zugrunde liegenden Ursachen in kurzer Zeit identifizieren und eine Reihe von Maßnahmen einleiten, um sie zu beheben – mit schnellen und signifikanten Ergebnissen. Die Materialverfügbarkeit stieg um fast 50 %, wodurch das Ziel des Klienten erreicht und ein wesentlicher Beitrag dazu geleistet wurde, die Zeitpläne wieder auf Kurs zu bringen.
Hintergrund
Mit der Eröffnung der neuen Produktion in Nordengland schuf unser Klient über 700 Arbeitsplätze in der Region. Der Schwerpunkt der Fabrik lag zunächst auf einem ersten Großauftrag, der den Bau von 173 Zügen umfasste.
Die Züge sollten im Ausland entworfen und in England von erfahrenen ortsansässigen Produktionsmitarbeitern gebaut werden. Um den Wissenstransfer in der Anfangsphase zu gewährleisten, sollten die neuen Mitarbeiter durch Kollegen der weltweiten Standorte des Klienten unterstützt werden. Das fehlende Supply-Chain-spezifische Know-how führte jedoch dazu, dass nicht immer zur richtigen Zeit die richtigen Teile an der Produktionslinie verfügbar waren – es kam zu Stillständen und Verzögerungen.
Da für das Überziehen der Lieferfristen hohe Vertragsstrafen vereinbart waren, war jegliche Verzögerung mit sehr schwerwiegenden Konsequenzen verbunden. Efficio wurde damit beauftragt, innerhalb möglichst kurzer Zeit die Probleme zu identifizieren und zu lösen, die zu den Verzögerungen geführt hatten.
Schnell wurde dabei klar, dass die Datenqualität eines der Hauptprobleme darstellte. Ein effektives Supply Chain Management war dadurch unmöglich. Aufgrund von Schwierigkeiten mit dem ERP-System des Werks gab es kein leistungsfähiges System für die Materialbedarfsplanung (MRP). Weiter verschärft wurde die Situation, da sich die verschiedenen Stakeholder nicht darüber einig waren, welche Supply-Chain-Prozesse wirklich relevant sind. Dies machte es sehr schwierig, die eigentliche Ursache für die Verzögerungen herauszufinden.
Darüber hinaus ergaben sich Probleme durch die Duplizierung von Teilen, also der mehrfachen Listung des gleichen Teils unter verschiedenen Artikelnummern, und dem Transport von Teilen zwischen Offsite- und Onsite-Lagern, weil es schwierig war, den zukünftigen Bedarf vorherzusagen. Die Mitarbeiter im Lager und in der Materialprüfung verbrachten oft Stunden damit, unterschiedliche Artikelnummern neu zu etikettieren und abzugleichen, um (vermeintliche) Engpässe an der Produktionslinie zu vermeiden.
Durch die Arbeit von Efficio erhielt der Klient vollständige Transparenz darüber, was die Verzögerungen verursachte und welche Maßnahmen ergriffen werden mussten. Mehr noch: Die gestarteten Initiativen konnten innerhalb sehr kurzer Zeit und unter hohem Druck erfolgreich das Problem der Materialverfügbarkeit lösen.
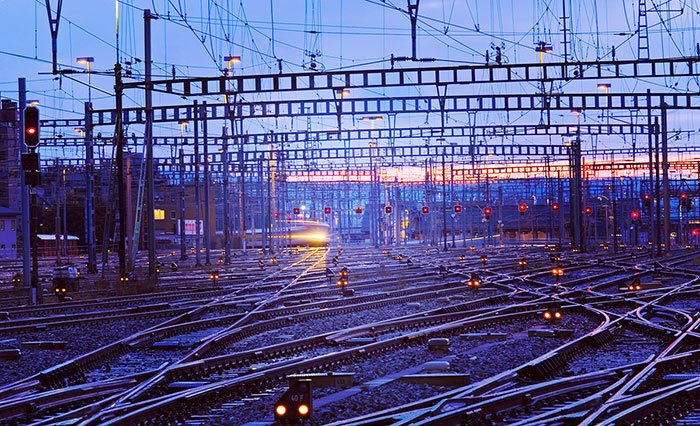
Ansatz
Efficio setzte sowohl Supply-Chain-Spezialisten als auch Branchenexperten ein. Dadurch wurde ein ganzheitlicher Blick auf die Lieferkette möglich und die zugrunde liegenden Probleme konnten identifiziert werden. Anschließend wurden in kurzer Zeit mehrere Initiativen zur Lösung dieser Probleme gestartet, beispielsweise:
- Verstärkung des Mitarbeiterteams des Klienten durch die Besetzung von Schlüsselpositionen wie Leiter Supply Chain und Leiter Materialprüfung mit Experten von Efficio, um unmittelbar Supply-Chain-Fachwissen und Know-how einzubringen. Dies erfolgte zusätzlich zu einem regulären Efficio-Projektteam vor Ort.
- Entwicklung und Implementierung einer Reihe von maßgeschneiderten Tools zur Lösung der Datenprobleme. Dazu zählte auch ein „Mini-MRP“-System für den Abgleich der Produktionsanforderungen mit der Materialverfügbarkeit. Zusätzlich wurde die Verfügbarkeit aller Züge über einen Zeitraum von 12 Monaten durch dieses System kalkuliert. Die Mitarbeiter in der Materialprüfung waren dadurch erstmals in der Lage, potenzielle Engpässe bereits zu erkennen (und zu beheben), bevor sie zu einem echten Problem wurden. Darüber hinaus entwickelte Efficio auch Tools, um die bisherigen Schwierigkeiten bei der Umlagerung von Artikeln zwischen Offsite- und Onsite-Lagern zu lösen.
- Bestandsoptimierung durch die Erstellung und den Einsatz eines warengruppenbasierten Prozesses für den Materialeinkauf. In diesem Zuge konnten fast 40 % der täglichen Kommissionierung auf ein Kanban-System überführt werden, wodurch erhebliche Ressourcen freigesetzt wurden.
- Eindeutige Klärung der Rollen und Verantwortlichkeiten für das Materialstammdaten-Team, wodurch signifikante Verbesserungen im Datenmanagement erreicht wurden. Efficio entwickelte zudem eine maßgeschneiderte Lösung für den Umgang mit doppelten Artikelnummern.
- Entwicklung einer KPI-Pyramide mit aufeinander aufbauenden Stufen. Dadurch wurde gewährleistet, dass alle Abteilungen auf das gleiche Ziel hinarbeiten.
Ergebnisse
Durch die Arbeit von Efficio erhielt der Klient vollständige Transparenz darüber, was die Verzögerungen verursachte und welche Maßnahmen ergriffen werden mussten. Mehr noch: Die gestarteten Initiativen konnten innerhalb sehr kurzer Zeit und unter hohem Druck erfolgreich das Problem der Materialverfügbarkeit lösen.
Die Materialverfügbarkeit stieg um fast 50 %, von 65 % zu Beginn der Beauftragung auf 95 % am Ende des Projekts. Damit wurde die Zielsetzung des Klienten erreicht und die mit Stillständen der Produktion verbundenen hohen Kosten konnten reduziert werden.
Die Beauftragung hat jedoch nicht nur das Hauptziel erreicht, sondern auch eine Reihe von fortlaufenden Vorteilen für den Klienten geschaffen. Die von Efficio entwickelten, maßgeschneiderten Tools schufen zeitliche Freiräume für die Mitarbeiter in der Materialprüfung und der Lagerhaltung. Dadurch war es diesen Mitarbeitern möglich, sich auf Problemlösungen in anderen Bereichen zu konzentrieren. Beispielsweise benötigte das Team im Lager für die Bestimmung des künftigen Bedarfs letztlich statt 1,5 Stunden nur noch weniger als zehn Minuten.
Zusammen mit dem durch Efficio eingeführten KPI-Prozess lieferten die Tools auch wichtige Management-Informationen, die bisher nicht verfügbar waren. Diese Daten unterstützen den faktenbasierten Ansatz von Efficio und werden vom Management des Werks auch weiterhin genutzt, um potenzielle Probleme zu identifizieren und entsprechende Lösungen zu finden.